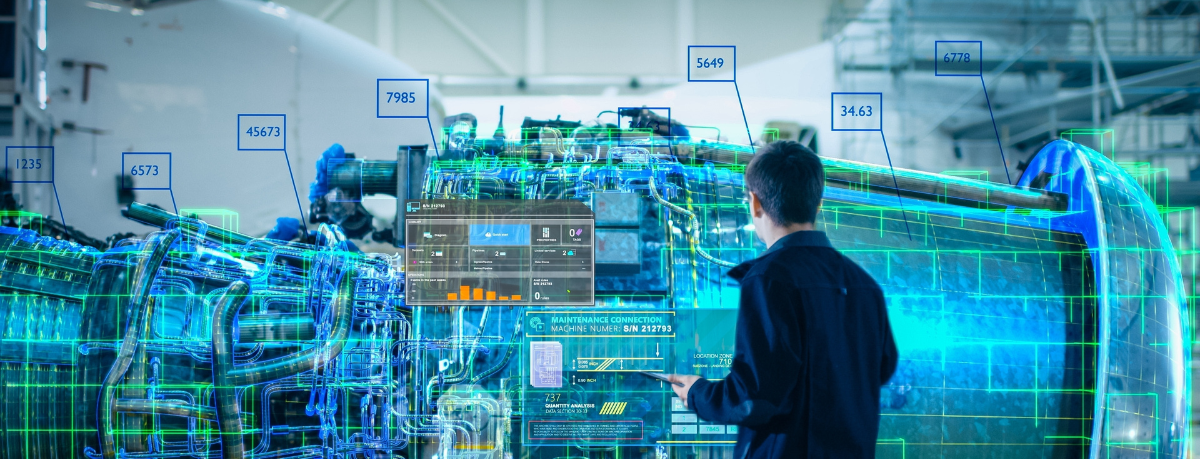
31 August 2023
Digital twin and Industry 4.0: let's clarify
In recent years we have talked a lot about artificial intelligence, internet of things, big data applied to Industry 4.0: but what happens when all these technologies are condensed into a single model that employs them in an integrated and simultaneous manner? This is where the digital twin comes into play!
What is a digital twin?
We often hear it mentioned, sometimes incorrectly or not at all, but what is the digital twin really? We speak of a digital twin when we are faced with a digital representation of an object, process or system existing and functioning in the real world. We therefore speak of a highly complex and dynamic virtual replica that exactly replicates its physical counterpart, which may be a product, a machine, a process, a building, a distribution network or even an entire ecosystem.
How does a digital twin work?
Some companies speak of a digital twin when they apply sensors to a process or product and, through them, monitor certain data. But is this really enough to be able to say that our company ‘uses a digital twin’? The answer is NO: a digital twin integrates data from sensors with mathematical models, algorithms and other sources of information, such as maintenance logs, operational data, images and videos. All in order to create an accurate, real-time representation of the corresponding, real-world object or process.
Why employ a digital twin?
The digital twin is a revolutionary tool for a company: it allows complex systems to be tracked and analysed more easily, both in real time and in the medium to long term, thus facilitating the optimisation of functions and processes (such as the supply chain and risk management), while at the same time identifying problems and correcting them before they have major implications or, in some cases, before they even happen.
Industrial applications and benefits
The digital twin can provide an integrated view of any project, to any user, at any point in the product lifecycle, enabling organisations to foster collaboration among various teams and departments, even outside the organisation. In addition to real-time monitoring, a digital twin can be used to perform simulations and analyses in the virtual world, test different conditions, scenarios and operations to understand how the real object would behave in different situations, but also to predict malfunctions and make informed decisions to improve efficiency. In the field of training, the digital twin can also be used to train personnel in a virtual environment, familiarising them with equipment and processes.
Among the main benefits of using a digital twin is therefore a general improvement in the efficiency of the company’s work, thanks to the possibility of making more informed decisions, improving efficiency and reducing risks. It also guarantees greater sustainability for the company.
Would you like to learn more about digital twins and whether it is an applicable solution in your company?
Our experts can help you understand whether your company is ready to innovate by introducing this or other Industry 4.0 technologies, study the department or process that could be digitally enhanced, and find the right technology partner for your needs. All this totally free of charge. Contact us and request an initial phone appointment.