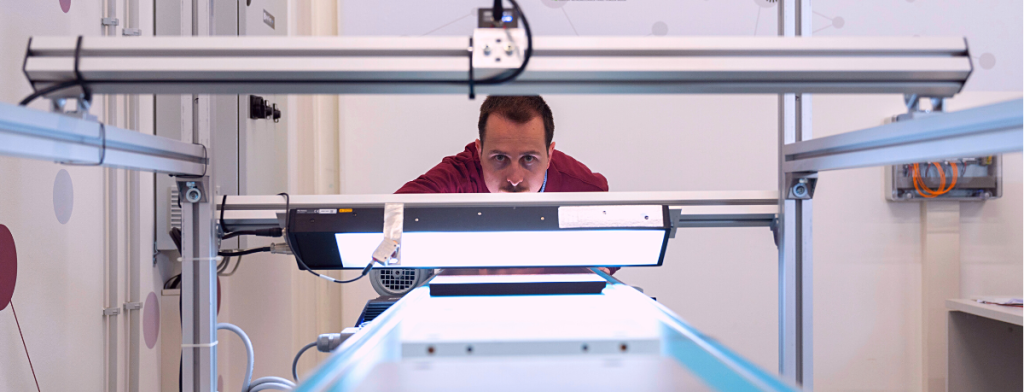
30 September 2022
Reducing production costs and improving quality control with new machine vision technologies
Can production be made more efficient to guarantee product quality and minimise waste and returns?
The answer to one of the most debated topics within companies when it comes to quality control is yes, thanks to Machine Vision tools. A technology that, through the use of cameras, optical systems and algorithms, obtains invaluable information for the optimisation of products and processes.
Too many realities still stuck with standardised controls
According to the findings of IP4FVG’s experts who assess the state of regional companies in relation to the technological, managerial and organisational aspects of Industry 4.0, there are still many companies in the region, especially SMEs, that rely on standardised quality control systems with obvious limitations and repercussions on the actual quality of products and the number of returns.
Traditional quality control involves visual and performance analyses on samples of semi-finished products carried out during the different stages of product processing. Most quality control in SMEs is performed by operators who track the progress of activities and report any anomalies. This is a control system with obvious limitations as it applies the results of the sample check to entire production batches, which may contain defective products which must be retuned with consequent additional costs for the manufacturing company.
Machine vision in quality control
New machine vision technologies, by means of cameras and optical systems generally installed along the production line, acquire images, detect product characteristics such as shape, size, edges, and process them through image processing algorithms to provide operators with precise information that helps optimise company processes and products.
The objective, for manufacturing companies implementing these systems, becomes that of monitoring in real time any deviations of the production process from the production requirements in order to minimise waste (zero defect production) by attempting to correct in real time the variables that generate variations in production and, where possible, automate certain processes, starting from product quality control on the individual pieces/components produced, for example by modifying the tasks of the operators and instructing the operation of any robots placed along the line that operate according to the data received.
Benefits and advantages of machine vision in quality control
The quality control benefits that the installation of machine vision systems brings to companies include:
- Reliability and continuity of controls
- The monitoring carried out by these systems can be performed on all parts, without any interference caused by a decrease in an operator’s attention threshold or other difficulties in terms of human-related performance.
- Speed in control
Monitoring takes place within fractions of a second, allowing the entire supply chain to be speeded up and with the possibility to activate a total production control system.
- Protection and reconversion of operators
The use of automatic vision systems protects operators from being present in environments that can generate situations of discomfort and stress (high noise levels, temperatures, presence of hazardous substances); their work can be reconverted to supervising and monitoring the measurements and analysing the data obtained.
- Test Accuracy
The software on which machine vision systems are based allows us to analyse even very small details, and detect errors within infinitesimal tolerance ranges.
- Limited impact on the existing production process
The currently-available technologies can be used on existing production lines without excessive impact on the existing process and with limited investment.
Test before invest: free Machine Vision technology demonstrator in Udine
In addition to Machine Vision technologies, a prototype for quality control, equipped with cameras and an embedded system for data acquisition, can be seen in the IP4FVG living lab in Udine (at the UNIUD HUB Village, Via Sondrio 2) as well as in the IP4FVG living lab in Amaro. This system detects the diameter of components online and transmits this information to the company’s platforms for subsequent analysis and processing.
To book a free visit, write to: contatti@ip4fvg.it